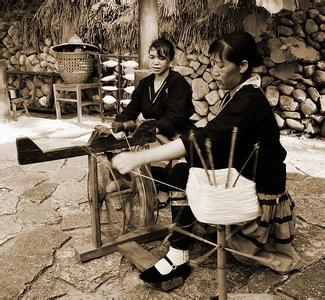
According to foreign media, as wages, energy and land prices in China and other Asian regions have risen, more and more Asian textile companies have moved factories to the southeastern United States in order to save costs. This has caused the textile industry, which has been declining for decades, to return to life. .
According to the report of the Wall Street Journal of the United States on December 20, Zhu Shanqing owned a spinning mill in Hangzhou, Zhejiang Province, China, and faced difficulties due to rising labor, energy, and land prices. He is packing some spindles into South Carolina. His company, Keer Group, intends to invest $218 million to build a factory in Lancaster County. Mr. Zhu said that the new factory's electricity bill is only half that of China, and it can get local government support. Kohl expects to create at least 500 jobs.
There is another benefit. As the cost of China continued to increase, Cole was able to ship the yarn to manufacturers in Central America. Unlike Chinese companies, it is duty-free to transport garments to the United States.
According to reports, the actions of Mr. Zhu and others will not allow the once prosperous southern textile industry to recover. But this shows how changes in global trade are creating advantages for U.S. manufacturing.
Robert Shit, Minister of Commerce of South Carolina states, “We are at the forefront of a mature cycle†and rising costs are driving Asian companies to migrate to the United States.
In September, China’s JN Fiber Company agreed to spend US$45 million to build a factory in South Carolina, processing plastic bottles into polyester fibers filled with pillows and furniture. The investment is expected to create 318 jobs. Economic development officials in South Carolina and Georgia say that Asian textile manufacturers that have approached them this year have increased.
The original textile mills that flourished in the United States were closed or relocated to less expensive countries in the 1990s.
The production cost of the textile industry in the United States is lower than that of China, India, Turkey, South Korea and Brazil. In 2012, Brian Hamilton, a doctoral student at North Carolina State University’s School of Textiles, wrote a doctoral thesis on the global textile industry. He said that rising costs have made spinning in China more expensive than in the United States.
He found that in 2003 spinning costs $2.86 per kilogram in the United States and $2.76 in China. By 2010, it will cost US$3.45 in the United States, and it will have risen to US$4.13 in China.
According to reports, the United States has imposed tariffs on imported yarn and clothing for several decades. But trade agreements such as the North American Free Trade Agreement created a tax-free zone between the United States and several trading partners. The relevant agreement stipulates that textiles imported from partner countries must be made entirely of materials produced in these countries or the United States, otherwise textiles will face customs duties, which can reach 5% to 6% for yarns and 10% to 12% for fabrics. %, Clothing is 15% to 20%.
Over the years, Asian garment manufacturers have endured such tariffs because production and transportation costs are low. And now, they are reassessing this practice.
The ShriVallabh Pittie Group in Mumbai, India, announced in October that it will invest US$70 million to build a textile mill in Georgia and provide 250 jobs. Company executives said that this is to avoid US tariffs and to obtain abundant, cheap and reliable energy. Another Alok Industrial Textiles Company in Mumbai announced in April this year that it will set up a spinning mill in the south of the United States to remove the U.S. tariff, and that electricity costs will be less than 10% of that in India.
Combined Fabrics Microfiber Fabrics Item
Combined Fabrics,Combined Fabrics Jobs,Combined Fabrics Owner,Combined Fabrics Careers
Changxing Zhongyuan Textile Co.,Ltd. , https://www.zyhometextile.com